Thermoplastic vulcanizates (TPV) below to the thermoplastic elastomer family. TPVs are chemically crosslinked rubber, mainly EPDM, in a thermoplastic polymer where the rubber may be partially or fully crosslinked. TPVs have the functional performance of conventional thermoset rubbers but with the processability of thermoplastics. TPVs have a number of excellent characteristics including excellent low compression set, good dynamic fatigue resistance, elastic recovery, temperature resistance, chemical resistance and easy processability. Typical applications for TPVs include seals and gaskets, CJV boots, wire and cable, tubing, pads and bumpers, food closures, grips and handles, weatherstripping, window glazing and automotive interior parts.
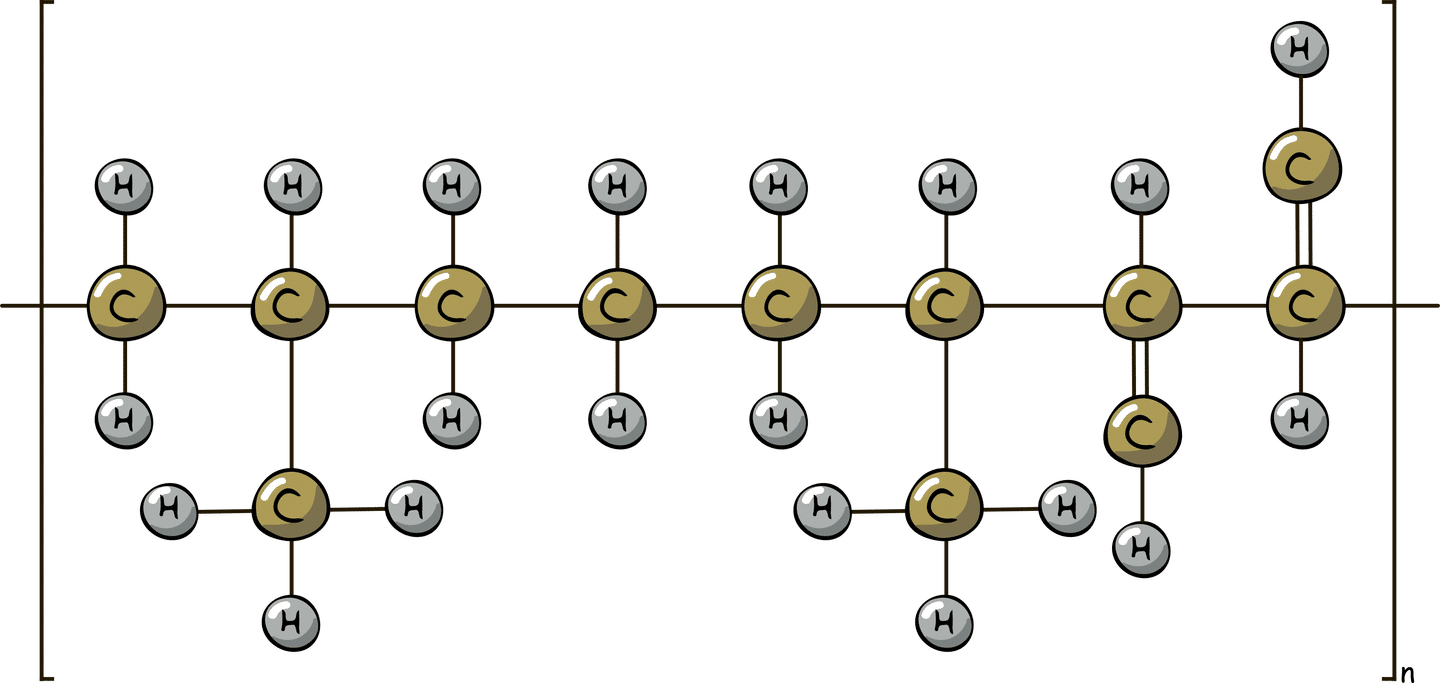
ABOUT
Polymer Characteristics
- Low Specific Gravity
- Low Compression Set
- Good Flex Fatigue Properties
- Good High Temperature Performance and Heat Aged Properties
- Broad End Use Temperature Range
- Good Chemical and Fuel Resistance
- Soft-Touch/Over-Molding/Bondable with Certain Substrates
- Wide Hardness Range, 25 Shore A to 50 Shore D
Grades
- General Purpose Grades
- FDA Food Contact Compliant Grades
- FDA Medical Approved Grades
- UV Stabilized Grades
- UL Approved Grades
- Flame Retardant Grades
- Bonding Grades
- Lubricated Grades
Processing Methods
- Injection Molding
- Extrusion
- Blow Molding
Typical Applications
- Automotive (Interior Surfaces, Weather Seals, Under the Hood Parts)
- Construction (Glazing Seals, Roof Sheeting, Road Expansion Joints)
- Appliances (Seals, Gaskets, Pads)
- Consumer Products (Housewares, Power Tools, Hand Tools, Toys)
- Industrial (Hoses, Belts, Seals, Gaskets)
- Electrical (Wire and Cable)
- FDA Food Contact and Medical Component Parts