Injection Molding Troubleshooting Tips
Tip #5: Short Shots
Short shots are molded parts that are not completely filled out. These are not only aesthetically unacceptable, they may also compromise the fit or function of the part.
From a material standpoint, potential causes of short shots could be using the wrong melt flow index (too low) material. Switching to a higher melt flow index could potentially resolve the problem. Another possible material cause could be over-drying the material, especially with nylon. If nylon becomes too dry its flowability goes down and could result in a short shot. For some other materials, if they are too wet it could cause screw slippage which could also result in a short shot.
From the machine standpoint one should ensure that heater bands and thermocouples are working properly and that the check ring is functioning. From a tooling standpoint one should ensure that gates and runners are of adequate size and are properly balanced. The mold vents should also be examined and cleaned if necessary. If any of these are not functioning correctly the end result could be short shots.
Lastly, the molding parameters can have a huge influence on short shots. If the melt and/or mold temperatures are too low the material will not flow as easily. If the injection speed is too slow, or possibly too fast, this too could result in short shots.
Again, all potential causes of short shots should be examined and investigated in order to determine the root cause and take the necessary correction actions to eliminate the defects.
Entec Polymers Technical Service Team
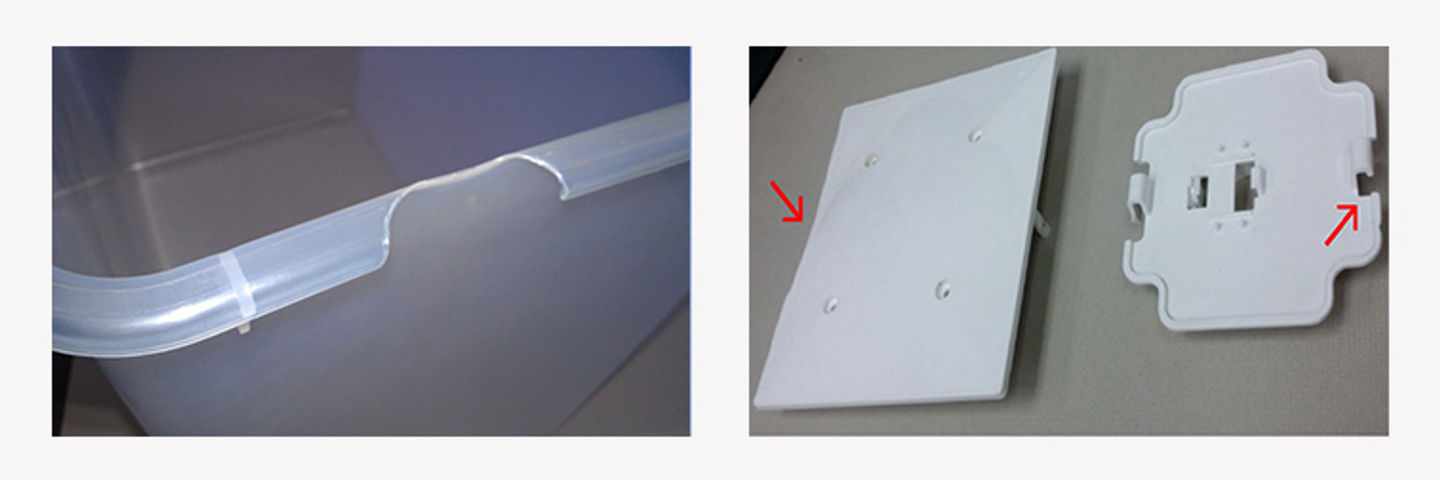