Injection Molding Troubleshooting Tips
Tip #6: Voids
Voids are a fairly common defect in thick wall injection molded parts and can be thought of as an ‘air pocket’. While voids are not visible on opaque parts, and can only be discovered by sectioning the part, they can easily be seen in transparent parts. Voids form when the outside layer of the part cools faster than the inner layer of the part. This causes the inner layer of the part to basically pull-apart causing the void to form.
While good part design dictates having a uniform wall thickness, sometimes thicker walls cannot be avoided. When this occurs, processing parameters will tend to have the biggest influence on minimizing or eliminating voids. Increasing the shot size, increasing injection pressure, and increasing hold pressure will tend to help the most. Increasing the mold temperature (to allow for better packing), decreasing the melt temperature and decreasing the injection speed may also help to minimize or eliminate voids.
From the tooling standpoint, the best remedy would be to increase the gate size or move the gate to a thicker section of the part. Increasing the size of cold runners might also need to be considered depending on the specific material being molded.
From the material standpoint, ensure that the material is dry to minimize any off-gassing due to moisture that could potentially contribute to voids. Switching to a lower flowing (higher viscosity) material should also be considered.
Again, all potential causes of voids should be examined and investigated in order to determine the root cause and take the necessary correction actions to eliminate this defect.
Entec Polymers Technical Service Team
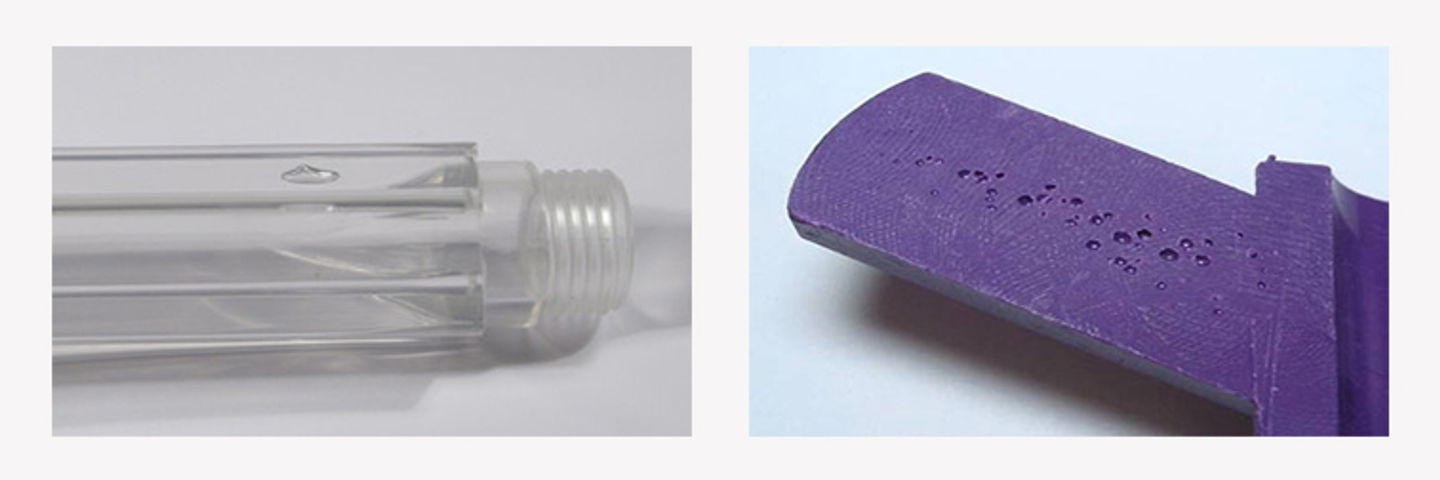