Learn More Now!
Download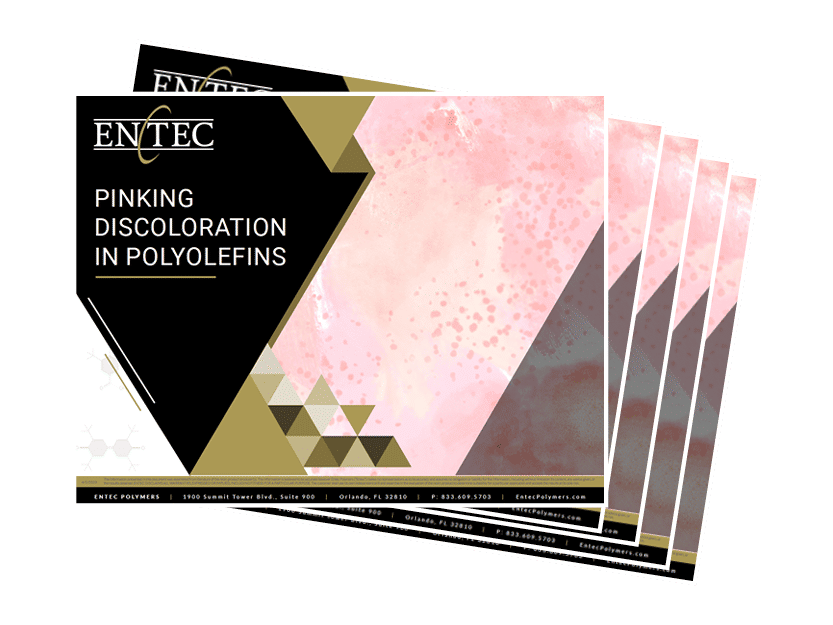
Learn more about our new customer portal
Customer PortalWhat is Pinking?
Pinking, yellowing and gas fade are all terms used to describe the same discoloration phenomenon. Typically seen in polyethylene, polypropylene and other polyolefin materials, although also possible in other polymers, this discoloration is usually caused by over- oxidation of phenolic compounds. Many polymers include phenolic-based antioxidants in order to help with processing and thermal stability of the material. These phenolic compounds will oxidize in the presence of NOx, SOx and other oxidation gases. A common source of these gases is the burning of a fuel, like from forklift trucks, natural gas or oil space heaters. This is why discoloration can be worse or occur faster in the winter months, when polyolefin materials and parts are exposed to these gases in a more enclosed warehouse or process environment. Some lower quality cardboards can also release SO2 over time, causing discoloration as well. Thankfully, this discoloration is cosmetic-only and does not affect the physical properties of the plastic.
Chemical Process
Phenolic antioxidants work by acting as sacrificial molecules. They donate hydrogen atoms in order to prevent free radicals from oxidizing the polymer instead. When a phenolic antioxidant is oxidized, it forms a quinone complex which ranges in color from yellow to pink. Pink is more common in light colored or white polymers as these colors often contain titanium dioxide and titanium-based quinones are pink in hue.
How to Avoid and Treat Pinking Issues
The discoloration that comes from these oxidation reactions is reversible. UV light changes the quinone structure such that it becomes colorless. How much UV light is required depends on your UV source (sunlight being most common), how severe the discoloration is and how close you place the parts to the UV source. Typically, at least 45 minutes minimum is required to reverse the discoloration.
There are also several methods to avoid pinking or yellowing from happening in the first place. First, avoid allowing plastic parts to sit for extended periods of time in warehouse storage. Ship parts from storage within about 90 days of molding to minimize the time the plastic parts are exposed to fork truck or heater fumes. If this is not possible, adding a plastic cover or wrap can help reduce the exposure to fumes as well.